The difference between forward and reverse osmosis?
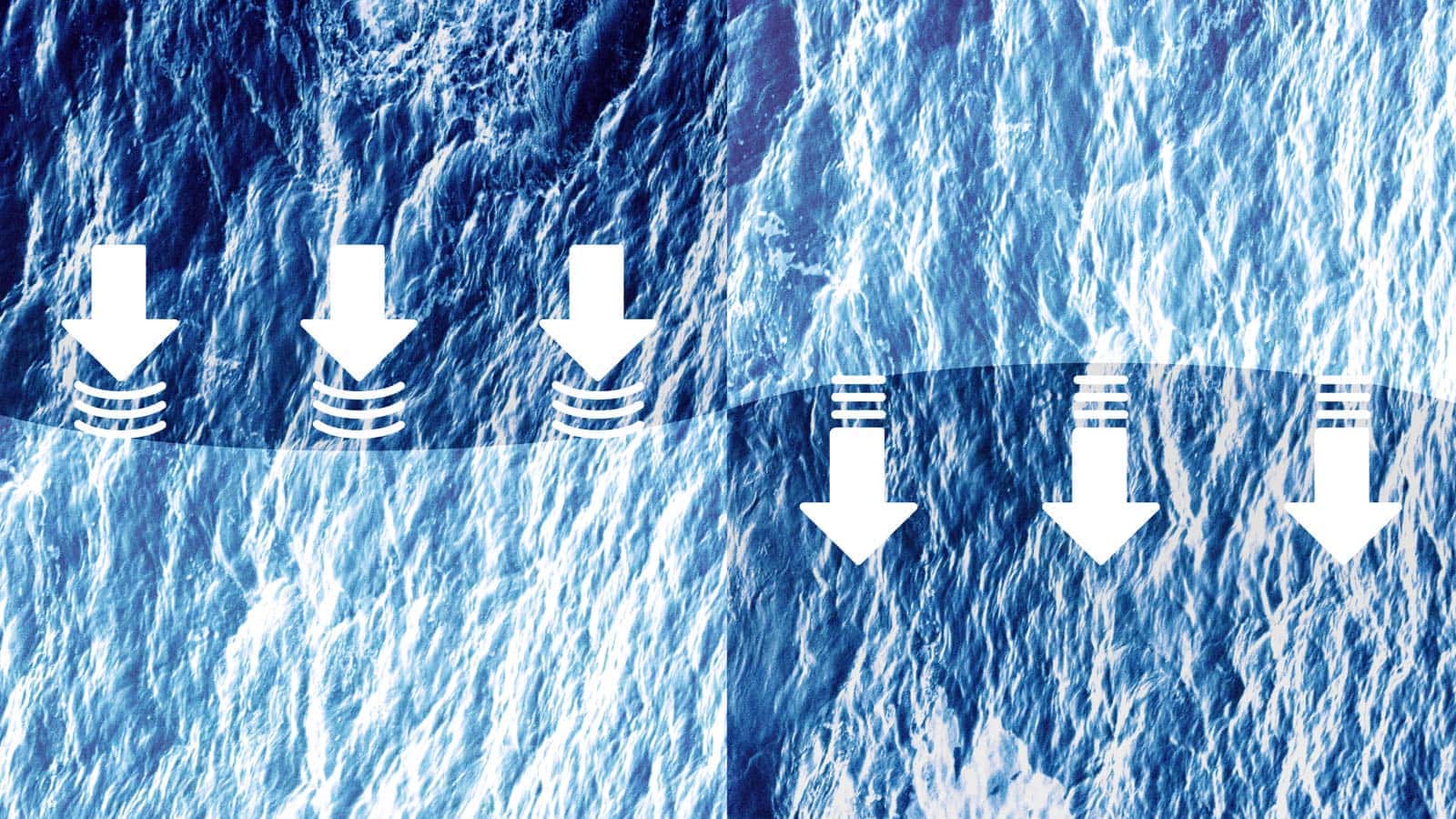
If you are a water professional or system integrator you are probably familiar with the benefits of osmosis when filtering wastewater. But are you aware of the differences between forward osmosis and reverse osmosis?
There are significant differences between forward osmosis (FO) and reverse osmosis (RO). When weighing the benefits of forward osmosis vs reverse osmosis for industrial effluent treatment, it is important to keep the strengths and weaknesses of each technology in mind. Both technologies are used to diffuse wastewater from one side of a membrane to the other, filtering out dissolved solids, ions, and other undesirable compounds in the process. But the main difference between reverse osmosis and forward osmosis is how water is driven through the membrane.
Forward osmosis vs reverse osmosis
In reverse osmosis, water is forced through the membrane using hydraulic pressure to overcome the natural osmotic pressure. The higher the salinity of the feed solution, the more pressure is needed. This requires high-pressure pumps and vessels with significant quantities of energy as a result.
Reverse osmosis also requires membranes that are suited for the specific task, such as brackish water membranes, seawater membranes, high-pressure or ultra-high-pressure membranes designed for an operating pressure ranging between 1,000 and 1,740 psi delivering a brine with Total Dissolved Solids (TDS) of up to 75,000 ppm. The feasibility of reverse osmosis normally starts to decline at brine TDS levels exceeding 75,000 ppm due to the pressure requirements.
Forward osmosis, on the other hand, uses natural osmotic pressure to induce the flow of water through the membrane by running a highly saline draw solution on the other side of the membrane. This means that the feed solution flows through the membrane at a relatively low pressure which eliminates the need for high-pressure hydraulics. This constitutes the main difference between forward osmosis and reverse osmosis.
Lower risk of scaling and fouling
A well-known issue with reverse osmosis membranes is fouling and scaling, where organic and chemical residue, oxidants, and scaling ions build up on the membrane surface. This reduces the effectiveness of the membrane and requires frequent maintenance and backwashing. Ideally, a reverse osmosis membrane should only handle water and pure salt, but with the complex composition of industrial wastewater effluent, this is rarely the case.
With forward osmosis, the low pressure of the feed solution makes the FO membrane less sensitive to fouling and scaling issues. This reduces the need for cleaning of the membrane and extends the lifetime of the membrane.
Osmotic Assisted Reverse Osmosis and Counter Flow Reverse Osmosis boosts forward osmosis
When using forward osmosis for brine concentration, you need a system to regenerate the draw solution and extract clean water for reuse. The most common way to recover water from a forward osmosis draw solution is by using reverse osmosis, which typically operates at 1,000 psi, or 70 bar. High-pressure reverse osmosis systems can push this limit further to 1,740 psi/120 bar, but here challenges with membrane and process stability arise. The salinity needed for an effective draw solution in many applications easily exceeds 100,000 ppm TDS, which makes it impossible to use traditional RO as a recovery method.
A more effective way to regenerate the draw solution is by using Osmotic Assisted Reverse Osmosis (OARO) or CounterFlow Reverse Osmosis (CFRO), which can help you achieve brine concentrations of up to 260,000 ppm TDS at half the cost of thermal evaporators. As contaminated effluent flows through the feed side of the forward osmosis membrane, the highly saline draw solution is responsible for extracting clean water through the draw side of the forward osmosis membrane. If that water is not continuously removed, the draw solution gradually becomes diluted and thus less effective as it loses its osmotic potential. This is why an effective draw recovery system is a key component of an FO system. It both extracts purified water for reuse and restores the TDS concentration of the draw solution.
With OARO/CFRO, it is possible to achieve draw solution concentrations of more than using less than 1,000 psi feed pressure. This eliminates the need for thermal evaporators for draw solution regeneration. The combination of forward osmosis and OARO/CFRO technology forms the perfect partnership for treating industrial wastewater with extreme levels of both TDS and Chemical Oxygen Demand (COD). By integrating forward osmosis with OARO/CFRO, you clear away the impurities with forward osmosis before the water reaches the OARO/CFRO system, which in turn delivers a top-quality draw solution that lets the forward osmosis system continue to function at peak efficiency.
Membrane quality is key
The difference between forward osmosis and reverse osmosis makes the two technologies suitable for different purposes. In both processes, the quality of the membrane is key. Aquaporin Inside® FO membranes use natural aquaporin proteins to filter water.
Aquaporins are the proteins responsible for transporting and purifying water in all living cells. Billions of years of evolution have made aquaporins super-efficient and super-selective, far better than any man-made water filter. Aquaporins are 100% selective to water molecules, which ensures that our forward osmosis membranes are highly efficient at rejecting chemicals, minerals, color, and other contaminants.
Aquaporin Inside® Forward Osmosis enables the efficient extraction of water, leaving behind challenging contaminants and reducing effluent volume. The process uses natural energy in the form of osmotic pressure to transport water through a filtration membrane, which improves efficiency without increasing energy use.
With Forward Osmosis you can:
- Minimize waste by effluent volume and sludge reduction to save costs related to disposal or evaporation/crystallization in Zero or Minimal Liquid Discharge systems.
- Reuse more water with better quality by treating streams with difficult contaminants and high BOD/COD/TOC – where other technologies fail.
- Simplify treatment through fewer and faster process steps by partly/fully replacing primary, secondary, and tertiary treatment – including chemical and biological treatments – to lower CAPEX/OPEX.
- Optimize land use through simpler and more efficient treatment which requires less space and can be easily retrofitted to your existing industrial facilities.
- Minimize maintenance and downtime as reduced fouling means less cleaning and fewer interruptions in your treatment.
- Turn your waste into profit when capturing precious materials in your wastewater - such as nutrients or metals – for recycling or reuse.
- Process more water without increasing your footprint in order to meet stringent industry requirements and your own environmental targets.
In essence, both forward osmosis and reverse osmosis can be used to solve pressing problems like water scarcity, industrial pollution, and a lack of water reuse. The two technologies each have their own place in an industrial wastewater treatment process.
Around the world, governments, industries and consumers are pushing for more responsible solutions that limit the use of water in industrial applications. From textiles to pharmaceuticals and heavy industry, our Aquaporin Inside® technology and membranes are a simple and cost-efficient way to streamline your water recovery processes and step up your water reuse. Whatever your wastewater challenge, our membranes and expertise can help you improve water recovery rates, reduce wastewater, and lower your expenses.
We hope you are now well-equipped to decipher the difference between forward osmosis and reverse osmosis.
Visit our industrial water page or contact us to discuss your industrial wastewater treatment needs and challenges.